Battery/EV
Home » Capabilities Overview » BATTERY/EV
Leading producers of production technologies for businesses in the battery and electromobility sectors include Patvin. We provide machinery for effective and superior battery and electric vehicle (EV) manufacturing along the value chain.
One of the main technologies for electric transportation is lithium-ion batteries. With cutting-edge technologies for solvent recovery as well as coating and drying electrodes, Patvin is well-represented in this significant, future-focused market. Fully automated cell and battery assembly technologies round out the offering. Our product offering also includes applications of thermal interface materials and testing technology for high-voltage circuits of electric vehicles at the end of the assembly line, in addition to technologies for bonding battery cells and modules.
Battery Cell Bonding
Bonding Solutions for Electric Vehicle Battery Cells
To provide insulation and protection against vibration and movement during the manufacturing process and throughout the life of the battery, cells within the battery pack or module need to be bonded together.
Depending on the battery design, cells also need to be bonded to a frame or cold plate. This helps dissipate thermal activity and keep contaminants out of the battery pack.
Bonding application sometimes varies by cell type
- Cylindrical cells are bonded to a polycarbonate carrier with two component or UV-cure acrylics.
- In prismatic cells, adhesive is dispensed in between each cell
- In pouch cells, hot melt pressure sensitive adhesive (PSA) is used to bond cells together and to frames or a cold plate.
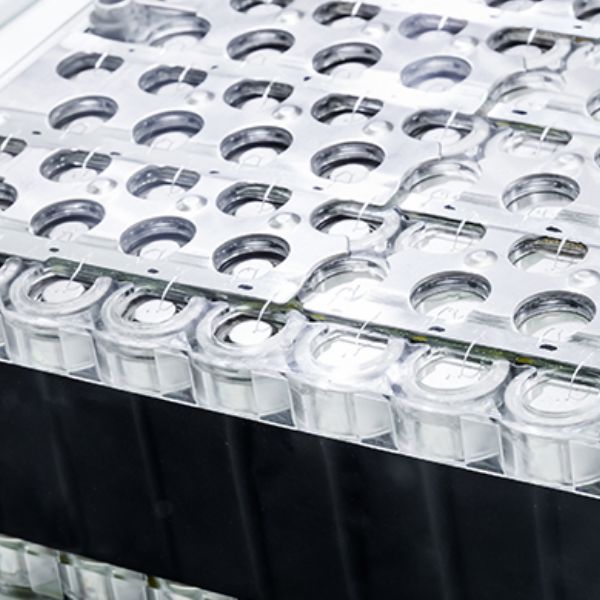
Cell to Carrier Bonding Stabilizes EV Batteries
In cell to pack bonding – also known as cell to carrier bonding – many cylindrical battery cells are fused onto a plastic carrier, keeping cells stationary at very short distances from each other. This allows the cells to maintain structural integrity while protecting them from vibration and movement during the welding process and life of the product.
Some advantages of Battery Cell bonding to customers are as below:
- Allows the cells to maintain structural integrity
- Provides insulation & protection against vibration
- Helps dissipate thermal activity
- Keeps contaminants out of the battery pack
Patvin Solutions
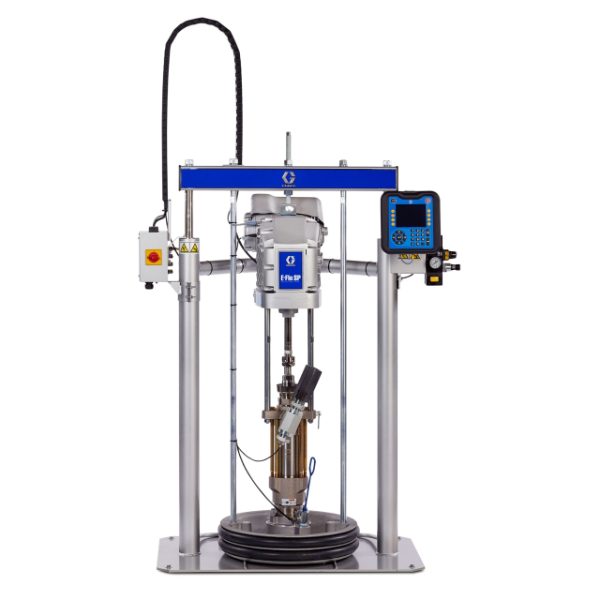
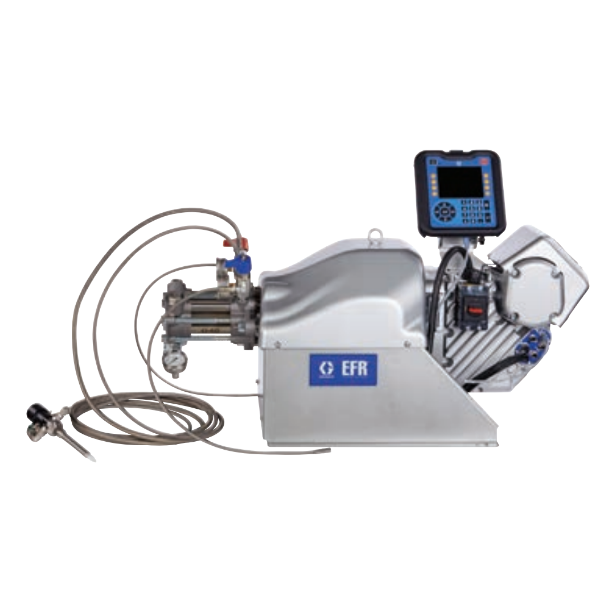
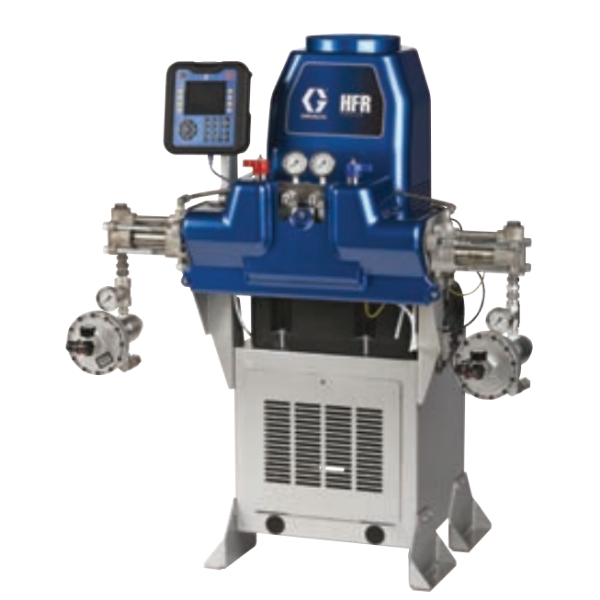
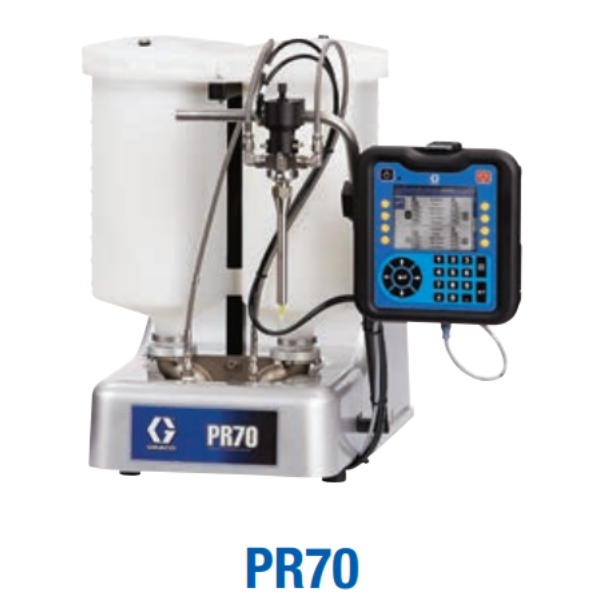
DIELECTRIC COATINGS
Dielectrics Mitigate Battery Fire Risk
When electric vehicles are in serious crashes, having surfaces that could conduct electricity coated with dielectrics reduces the potential for a fire.
For dielectric coatings to prevent arcing or breakdown voltage, these components must work together:
- the right material or chemistry
- the ability to mix and spray that chemistry on ratio at a consistent flow rate
- an automation technique that handles specific part geometries
If all three do not work together while manufacturing EV batteries, you’re likely headed for trouble.
Patvin Solutions
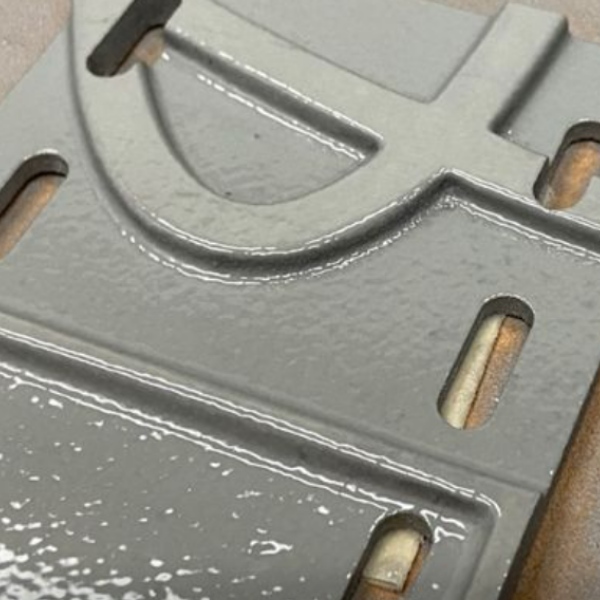
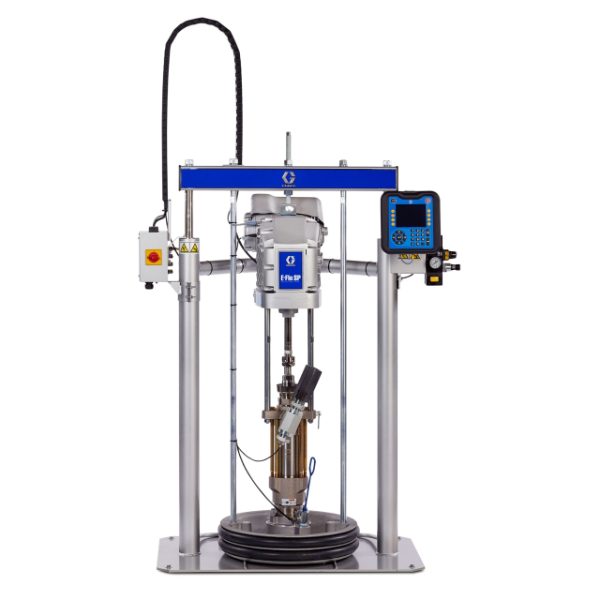
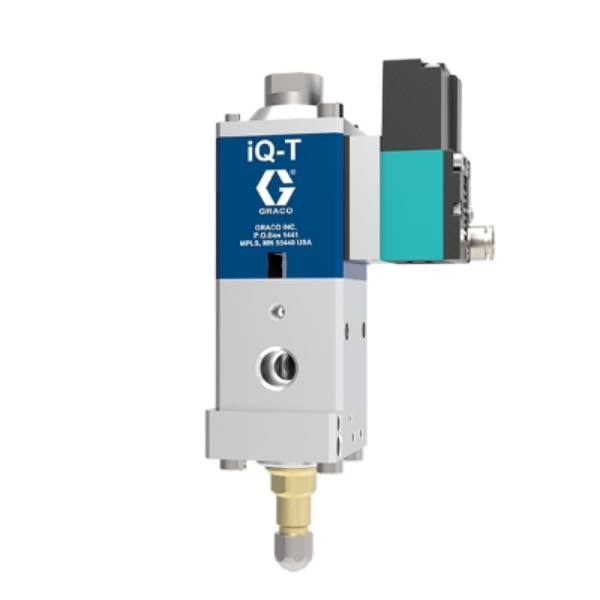
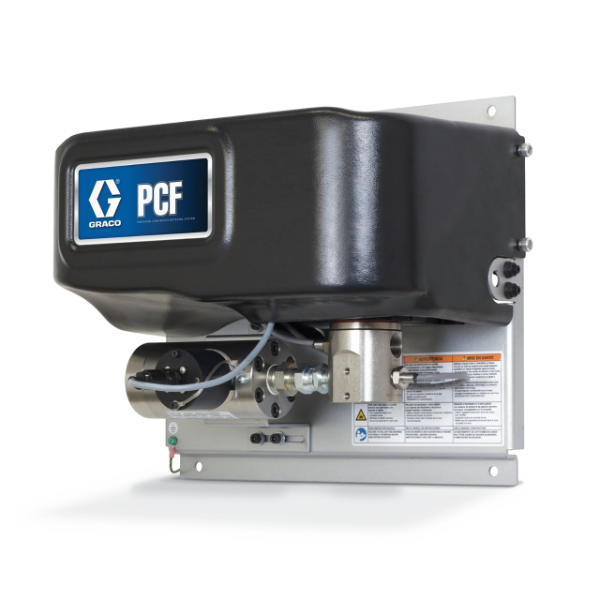
FIREPROOFING
Passive Fire Protection with Intumescent Coatings
Originally used in construction, passive fire protection (PFP) or intumescent coatings are rapidly moving into the automotive space. Applying a thin, even layer of a PFP epoxy, polyurethane, or silicone to the outside of a battery pack protects it from extreme heat.
When a certain temperature is reached, the sprayed layer of intumescent coating expands, insulating the battery. This keeps the thermal event from reaching the passenger compartment of an electric vehicle (EV).
So that intumescent coating provides effective fire protection, the following must happen:
- Keep the high viscosity material at the correct temperature when being mixed.
- Dispense it at a continuous flow for reliable application.
- Monitor closely the mixing ratio.
Patvin Solutions

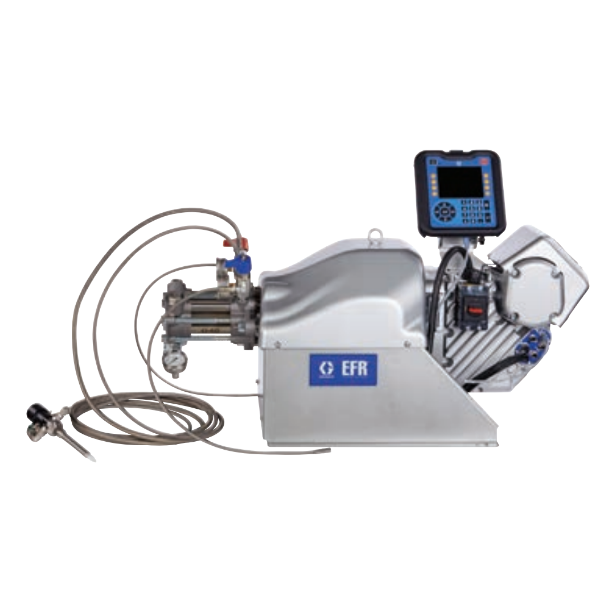
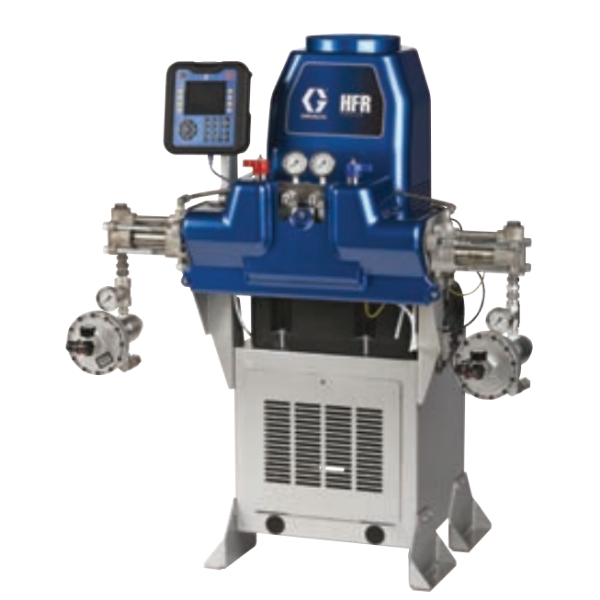
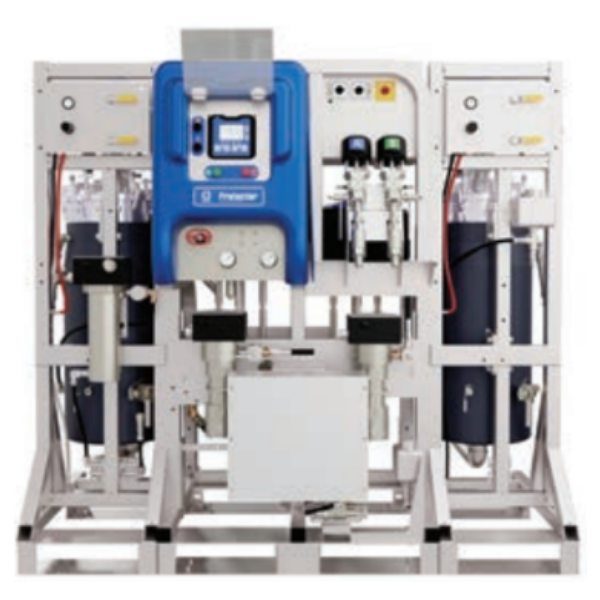
BATTERY ENCAPSULATION
Insulating and Protecting Battery Cells
Foam encapsulation can add structure and rigidity to the battery pack by holding cells in place to protect them from shocks or vibrations. This is typically done using two component materials like silicone, silicone foam, epoxy, epoxy foam and polyurethane foam.
Encapsulation foams are mixed and dispensed into a module to fill the spatial cavities between each cell. The extra stability increases thermal insulation and prevents thermal runaway.
Patvin Solutions for Battery encapsulation
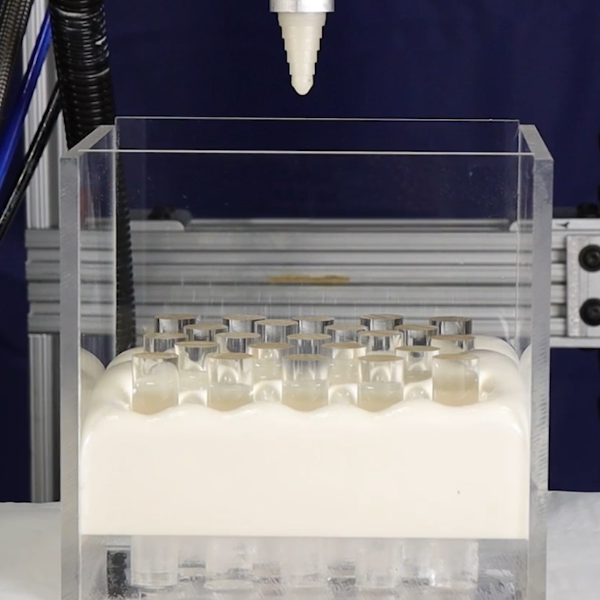
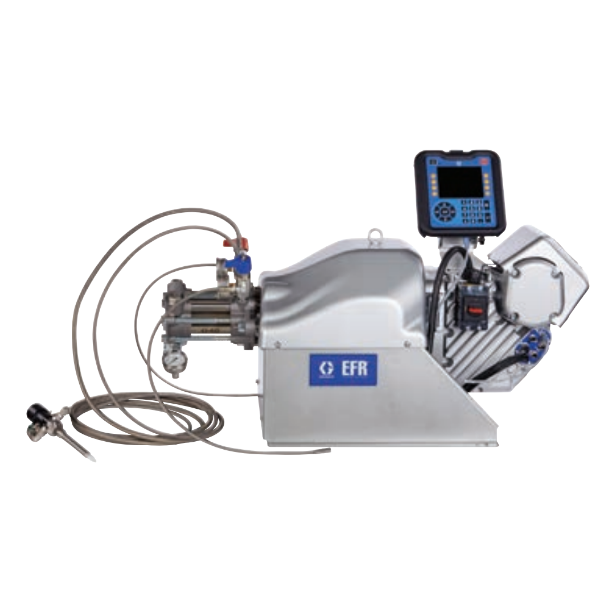
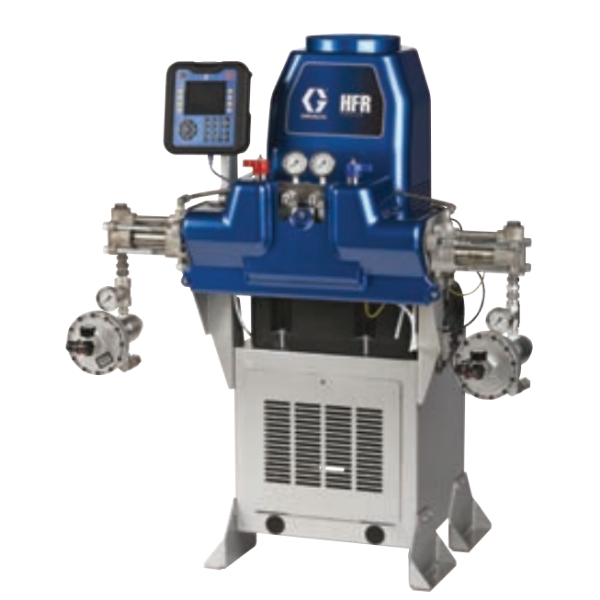
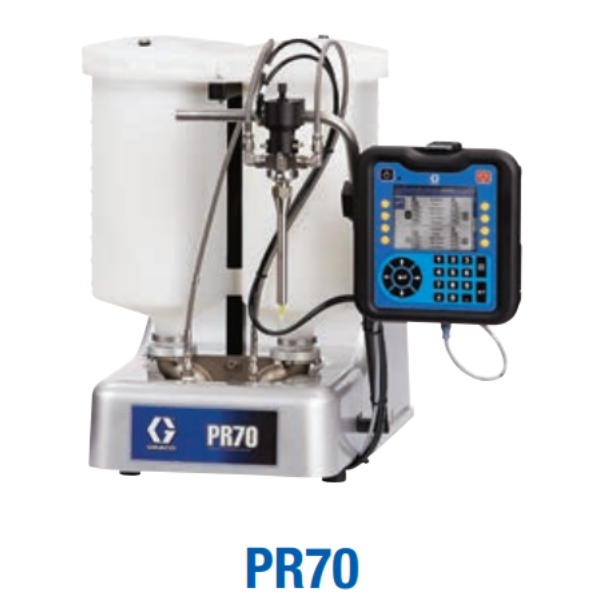
PACK SEAL
Solutions for Sealing Battery Packs
Achieving a quality seal is critical for the performance, longevity, and protecting components of the battery from water and other harsh environmental conditions.
Battery pack seals or gaskets must meet design and regulatory enclosure standards. For example, an IP68 rating means that the seal will protect against water intrusions, corrosion, and outside contaminants.
Manufacturers meet these standards by robotically dispensing a bead of one or two component material around the perimeter of the battery pack in one of two ways:
Cure in place gasketing (CIPG): The dispensed material cures before assembly, creating a compression gasket in the pack seal joint.
Form in place gasketing (FIPG): The material is dispensed and assembled immediately, allowing the material to cure over time.
To ensure a durable, reliable seal, gasketing must be clean, precise and repeatable. Bead placement, flow rate, volume of material dispensed, and mix ratios for two component materials are critical.
Customer advantage –
- Critical for the performance, longevity, and overall protection
- Protects against water intrusions, corrosion, & outside contaminants
Patvin solutions-
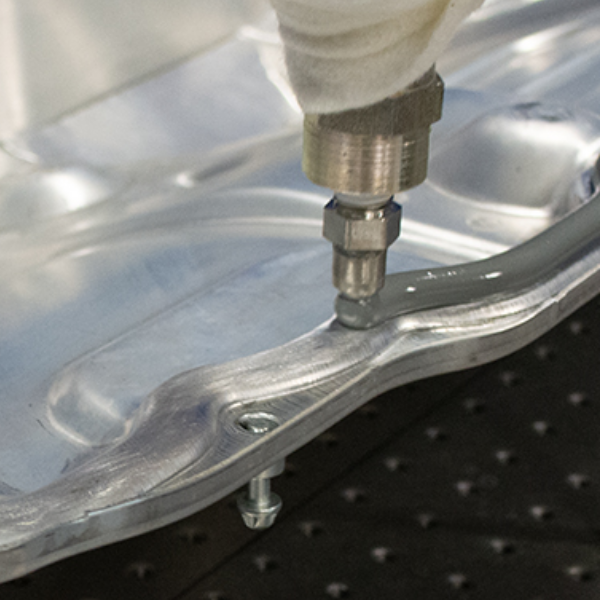
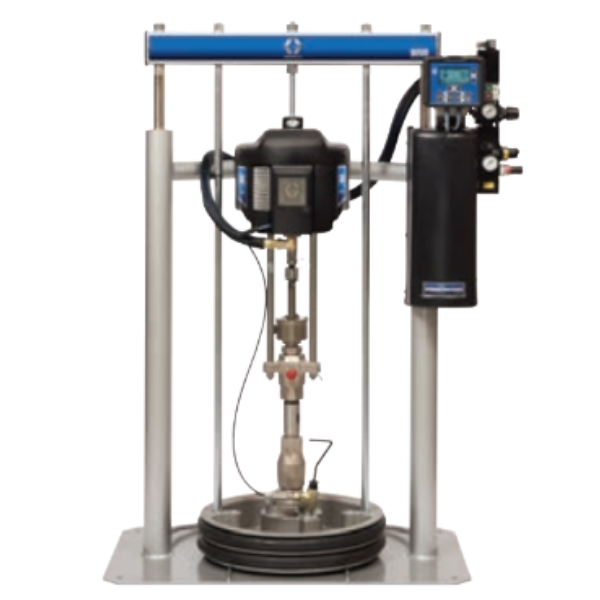
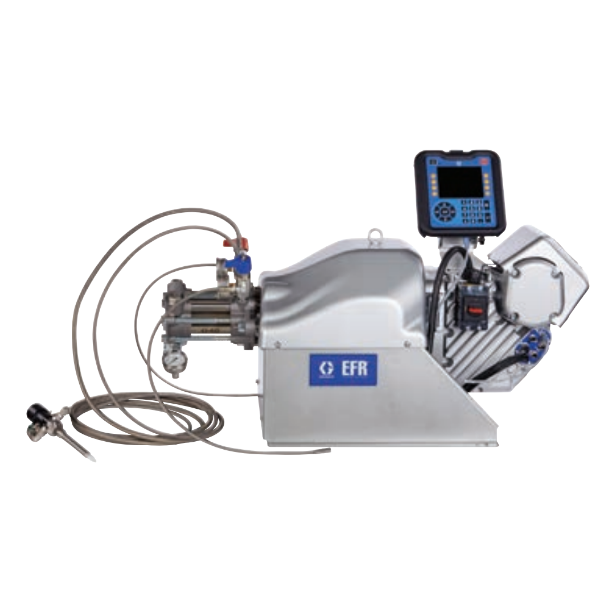
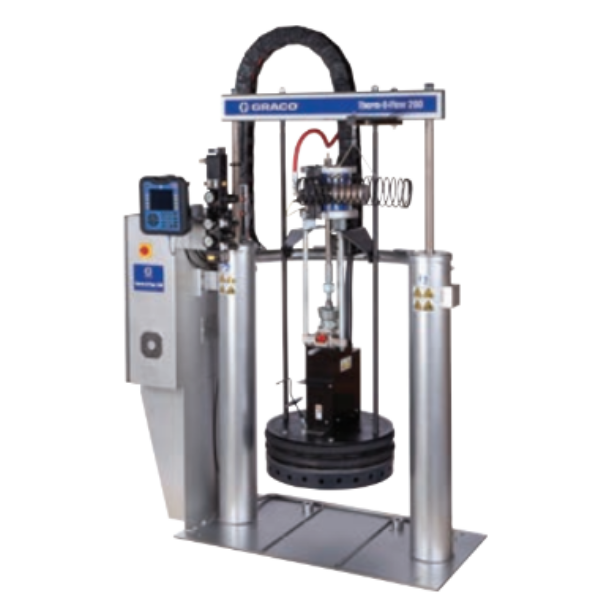
STRUCTURAL BONDING
Proper Adhesive Application for Strong and Light Battery Packs
Using adhesives for structural bonding methods help make a battery lightweight, while adding strength and rigidity. Typically, a one or two component epoxy is dispensed in a bead shape to bond two pieces of a battery pack together.
Precision and accuracy are important to proper bonding and efficient material use. Metering systems with strong material control and robust equipment to handle highly abrasive, medium to viscosity material is recommended.
Customer advantage of structural bonding:
- Helps make a battery lightweight
- Offers extra strength and rigidity to the battery pack
- Vibration and Fatigue Resistant
Patvin solutions for structural bonding
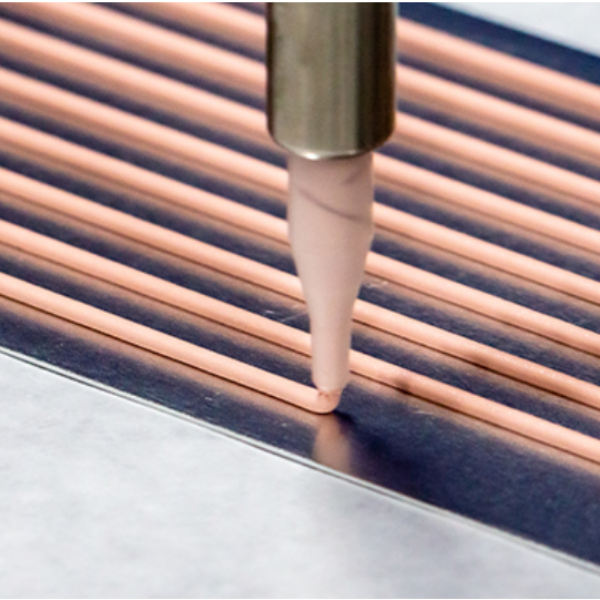
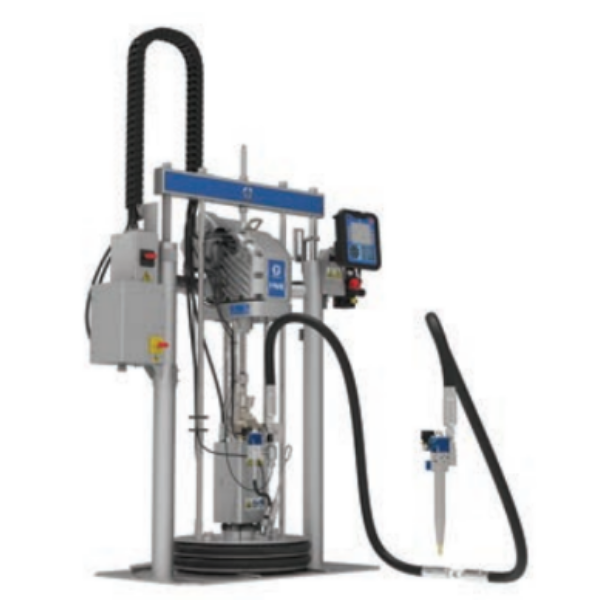
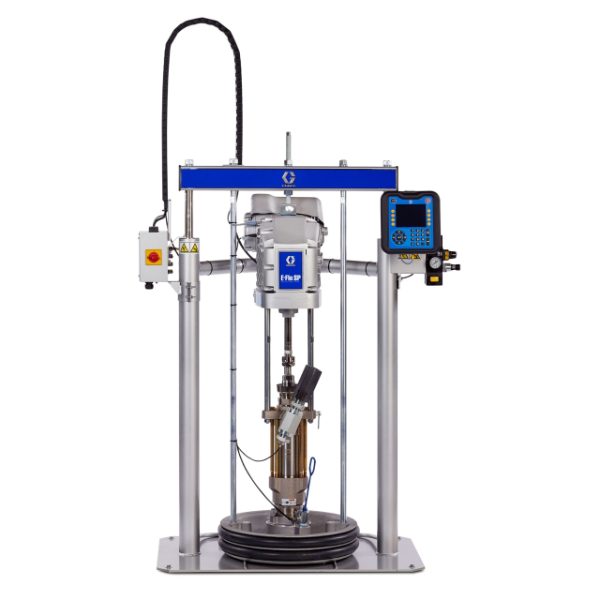
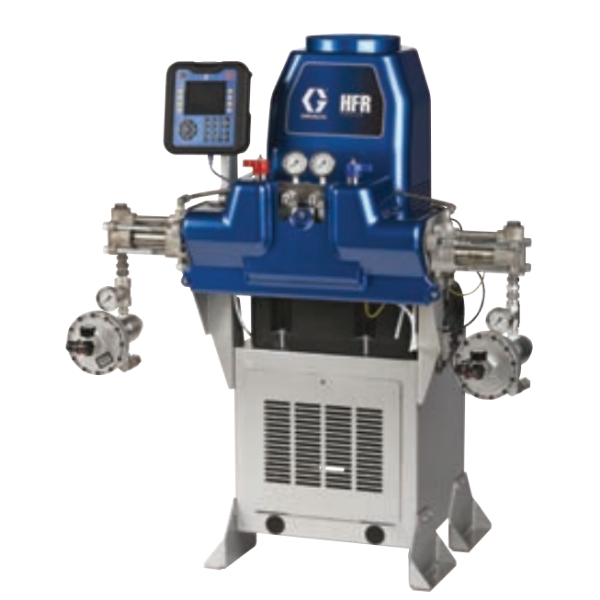
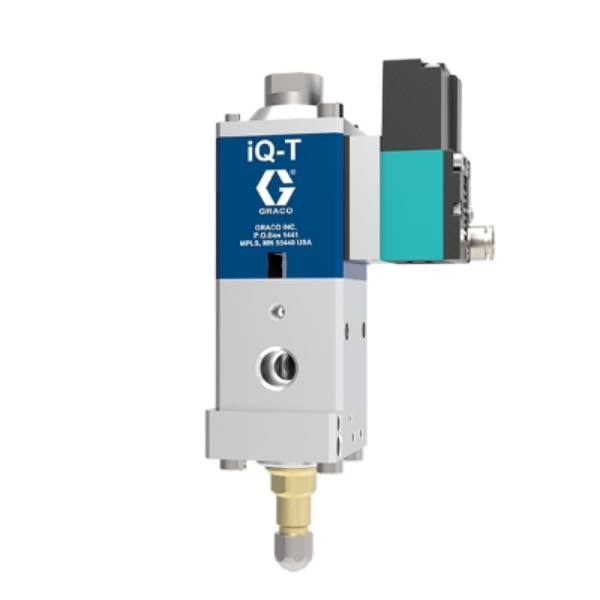
THERMAL MANAGEMENT (GAP FILLER)
Handling Highly Abrasive Thermal Interface Material
Thermal interface materials used in gap filling applications are critical to overall battery performance and safety. When dispensed correctly, the gap fillers dissipate heat away from the battery, improving battery speed, longevity and decreasing the likelihood of thermal events.
However, pumping and dispensing thermal interface material (TIM) brings many challenges to electric vehicle (EV) battery assembly lines. Highly abrasive and low viscosity in nature, the gap filler can quickly wear out equipment. TIM also needs unique attention to pressurization to ensure optimal heat transfer.
To withstand this tough material, manufacturers should consider robust equipment that allows for high flow, precise metering and dispense.
Customer advantage:
- Critical to overall battery performance and safety
- Dissipate heat away from the battery
- Improves battery speed & longevity
- Decreases the likelihood of any thermal events
Patvin Solutions
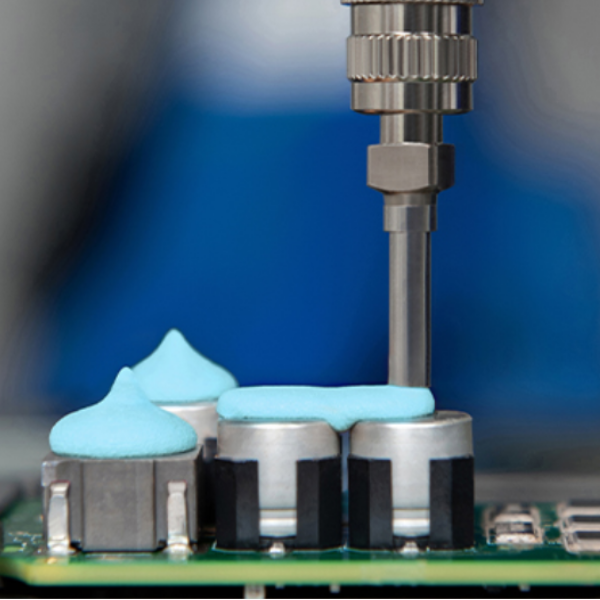
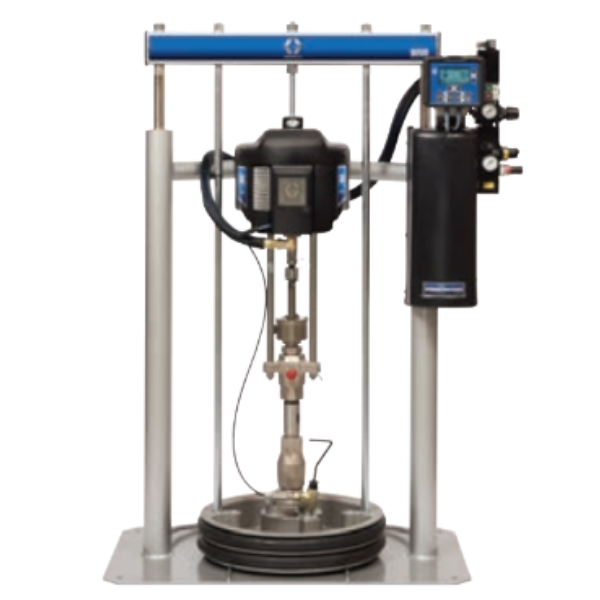
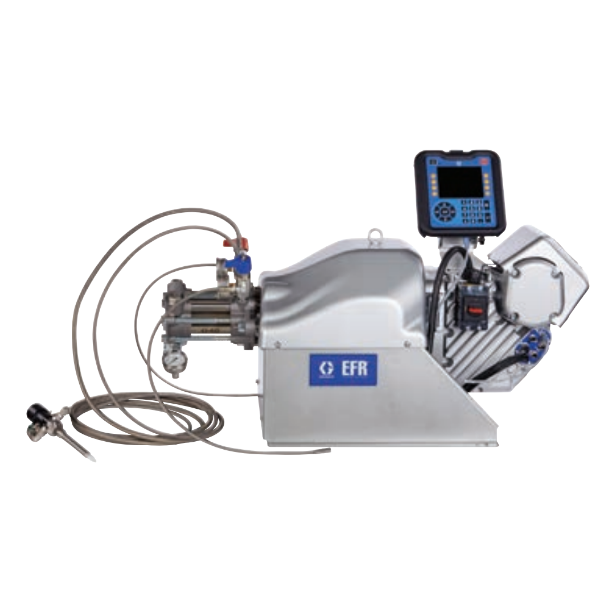
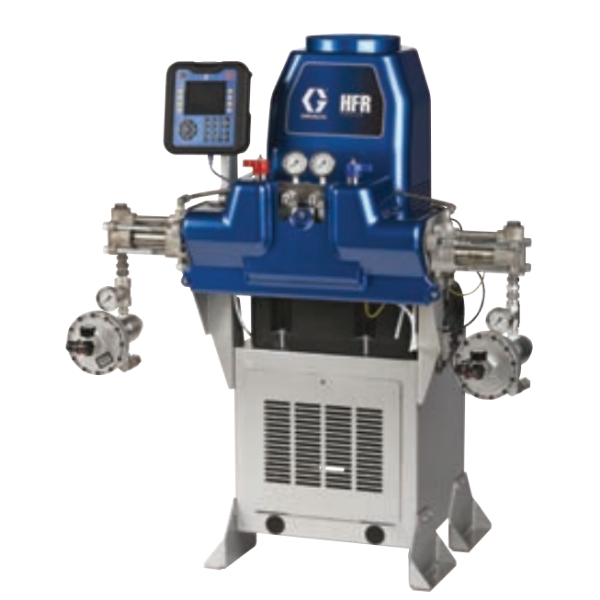